Dai quite correctly advised not to use stainless steel bolts in high stress areas - here's why.
It is ususal these days to measure both stress as well as pressure in N/mm2
or Ton force/sq" - 1N (newton) is approx. equal to 0.225 lbf (pound force).
The following figures give the UTS (ultimate tensile strength - ie. failure) and the Yield strength (permanent elongation) of commonly available bolts.
Mild Steel:- UTS = 500-550 N/mm2 (32-35 Tonf/sq")
Yield = 110-160 N/mm2 (18-23 Tonf/sq")
Stainless Steel (18/8 ):- UTS = 800 N/mm2 (51 Tonf/sq")
Yield = 580 N/mm2 (36 Tonf/sq")
HT steel:- UTS = 1180-1370 N/mm2 (75-90 Tonf/sq")
Yield = 1060 N/mm2 (68 Tonf/sq")
Note that a HT bolt yields at almost double the stress of a S/S one!!!
The keeper of obscure facts.
HT bolts verses S/S
I've edited it for you mate
If you put and "8" followed by a bracket... it reckons you want a pimp smilie... a la

If you put and "8" followed by a bracket... it reckons you want a pimp smilie... a la

'89(G) 340 GLE B172k
'03 S60 D5 SE, '91 (J) MX5, 1954 Cyclemaster
Ex:
'89(F) 340 GL F7R (ex B172k) - Fake -> SBKV 300 Runner Up 08, 12; '91(H) 340 GL B14.4E - Kar; '88(F) 360 GLT B200E - Jet -> BKV 300 Runner Up 09; '89(G) 360 GLT B200E - Beast
'03 S60 D5 SE, '91 (J) MX5, 1954 Cyclemaster
Ex:
'89(F) 340 GL F7R (ex B172k) - Fake -> SBKV 300 Runner Up 08, 12; '91(H) 340 GL B14.4E - Kar; '88(F) 360 GLT B200E - Jet -> BKV 300 Runner Up 09; '89(G) 360 GLT B200E - Beast
Very true. There's also different grades of high tensile steel. Most fixings are 'bog standard' 8.8 grade. Moderately strong stuff such as the brake caliper bolts are grade 10.9 and very highly stressed stuff such as flywheel mounting bolts were even higher 12.9, which I believe is pretty well as high as you can go.
There is an engineering meaning to the grades. I don't fully understand it but its something along the lines of: the first number is 100th the 'nominal tensile strength' in N/mm2 and the second number is ten times the ratio between the tensile strength and the yield strength in N/mm2. The numbers Mac gave you in his last column would probably most closely relate to a grade 12.9
There is an engineering meaning to the grades. I don't fully understand it but its something along the lines of: the first number is 100th the 'nominal tensile strength' in N/mm2 and the second number is ten times the ratio between the tensile strength and the yield strength in N/mm2. The numbers Mac gave you in his last column would probably most closely relate to a grade 12.9
Last edited by pettaw on 15 Nov 2006 08:08 pm, edited 1 time in total.
-
- *** V3M DONOR ***
- Posts: 5465
- Joined: 25 Apr 2005 06:52 pm
- Location: Anglesey North Wales
- Contact:
There also a few different grades off s/s bolts.
Dai
Please email me directly on dai@classicswede.co.uk
http://www.classicswede.com
phone/text 07824887160
Web shop http://www.classicswede.co.uk/
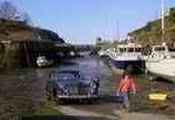
Please email me directly on dai@classicswede.co.uk
http://www.classicswede.com
phone/text 07824887160
Web shop http://www.classicswede.co.uk/
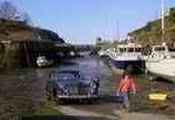
Mode of failure is also an issue. Stainless does not "yield".
And the thing most people do not understand is that a properly designed bolt acts like a spring. If there is no stretch then it will be unreliable in service: more likely to come loose. That means less strength can be better. (Still talking carbon and low alloy steel here, not stainless.) Changing from 8.8 to 10.9 or 12.9 is not always a good thing.
The reason its called stainless is because that is its most important property. Most of its other properties are rubbish.
Yet another golden rule for good bolt design is not to listen too much to anyone in the oil & gas industry. Bolting there tends to be based on American ideas/misconceptions and is not the best. The motor industry is general top notch on bolted joint design and they buy in such huge quantities that costs are always low so dont go changing unless you have a really good reason.
Correct grade, correct surface treatment, correct torque, minimum use of washers and enlightened use of anaerobic adhesives will provide good results.
And the thing most people do not understand is that a properly designed bolt acts like a spring. If there is no stretch then it will be unreliable in service: more likely to come loose. That means less strength can be better. (Still talking carbon and low alloy steel here, not stainless.) Changing from 8.8 to 10.9 or 12.9 is not always a good thing.
The reason its called stainless is because that is its most important property. Most of its other properties are rubbish.
Yet another golden rule for good bolt design is not to listen too much to anyone in the oil & gas industry. Bolting there tends to be based on American ideas/misconceptions and is not the best. The motor industry is general top notch on bolted joint design and they buy in such huge quantities that costs are always low so dont go changing unless you have a really good reason.
Correct grade, correct surface treatment, correct torque, minimum use of washers and enlightened use of anaerobic adhesives will provide good results.